In-House Component Manufacturing
Thacker manufactures many of its key casket-related components under its own roof in Florence, Alabama. Producing its own casket-related components has allowed Thacker to control both the cost and the quality of the components. In addition, it has ensured Thacker’s long-term independence from other manufacturers in the market while keeping additional American workers employed!
Steel Stamping
In 2019, Thacker built the industry’s newest steel casket stamping facility in the U.S. Thacker stamps its steel parts in a new 40,000-square-foot building that is attached to its existing casket assembly buildings. Thacker stamps its metal parts on three presses purchased from the Ford Motor Company. Each press has the capability of generating 1,000 tons of force. In developing its own stamping facility, Thacker also designed stamping dies that form the major steel components including long sides, short ends, the lid, and other components such as the header. In stamping its own parts, Thacker has ensured its long-term future for sourcing this critical metal casket component.
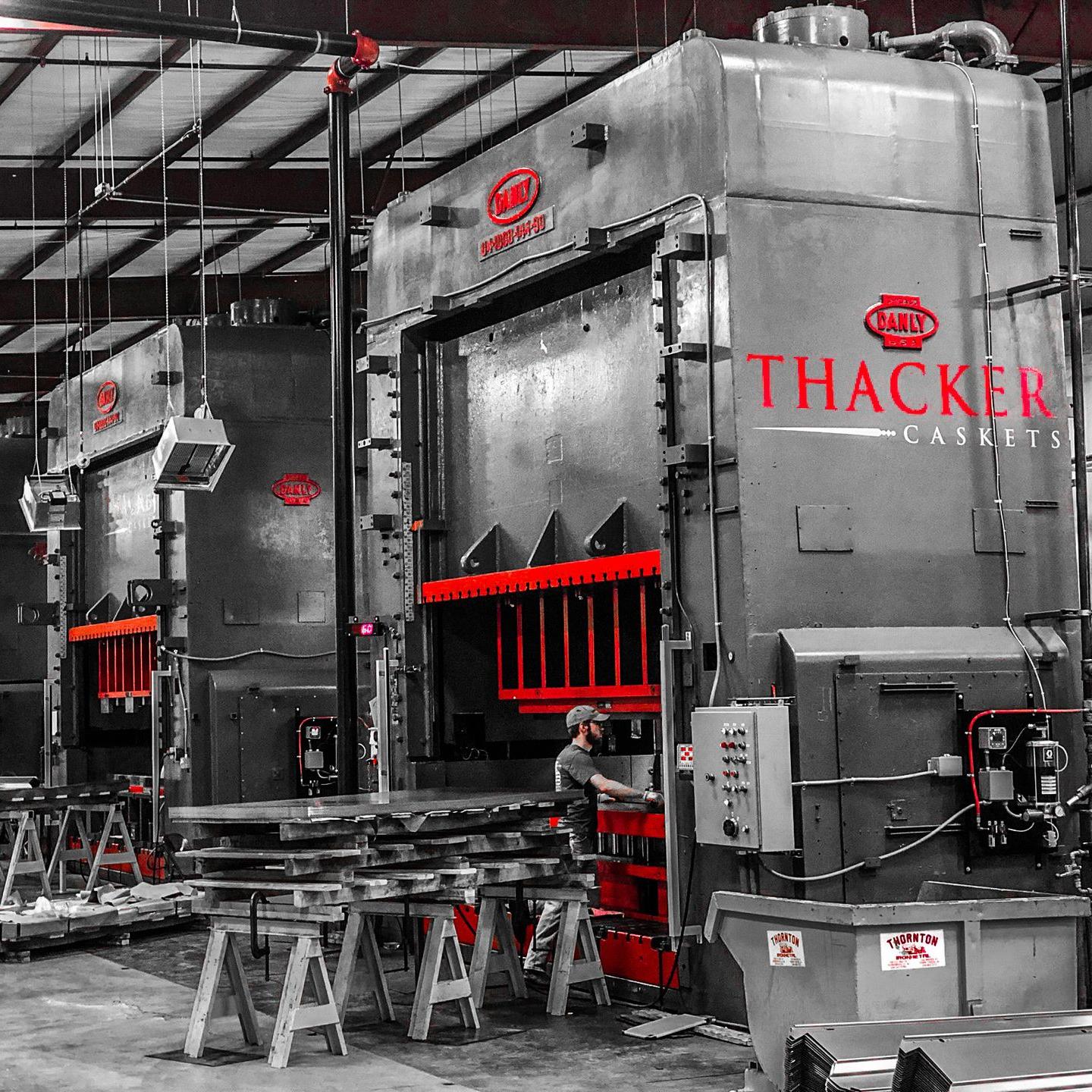
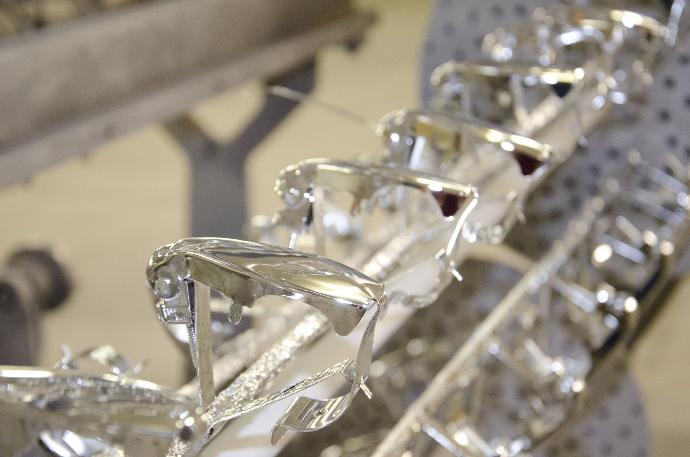
Hardware Manufacturing
In 2009, Thacker started an initiative to begin producing its own casket hardware. Thacker first began by producing its simple sets of stationary bar hardware, then moved on to producing more intricate swing-bar styles. Currently, Thacker makes its own hardware for approximately 80% of the caskets that the manufacturing plant produces. All of Thacker’s hardware is produced via plastic injection molding whereby poly-carbonate plastic pellets are melted and then injected into a mold. From there the mold of the corners or handle pieces are formed as the plastic cools. The parts are then ejected from the molding machine. Some parts will undergo additional processes called “plating” to create a shiny look. These parts will be vacuum metalized which is a process that coats the parts via vaporizing aluminum. The parts then are tinted, for color, and a clear coat is applied. Thacker also produces its own casket handlebars using a form rolling machine.
Bed Manufacturing
In 2020, Thacker purchased long-time industry supplier, Miller Berry who supplied the industry casket beds for decades. Thacker moved all of Miller Berry’s equipment from New Jersey to Alabama where Thacker brought the bed manufacturing under the same roof as its casket assembly. Purchasing Miller Berry has allowed Thacker to continue to control its quality and also make product improvements to the casket beds as necessary. One of the benefits of Thacker’s casket beds is the fact that they are built to be wider than the industry standard bed to allow a funeral director to better position the decedent for viewing.
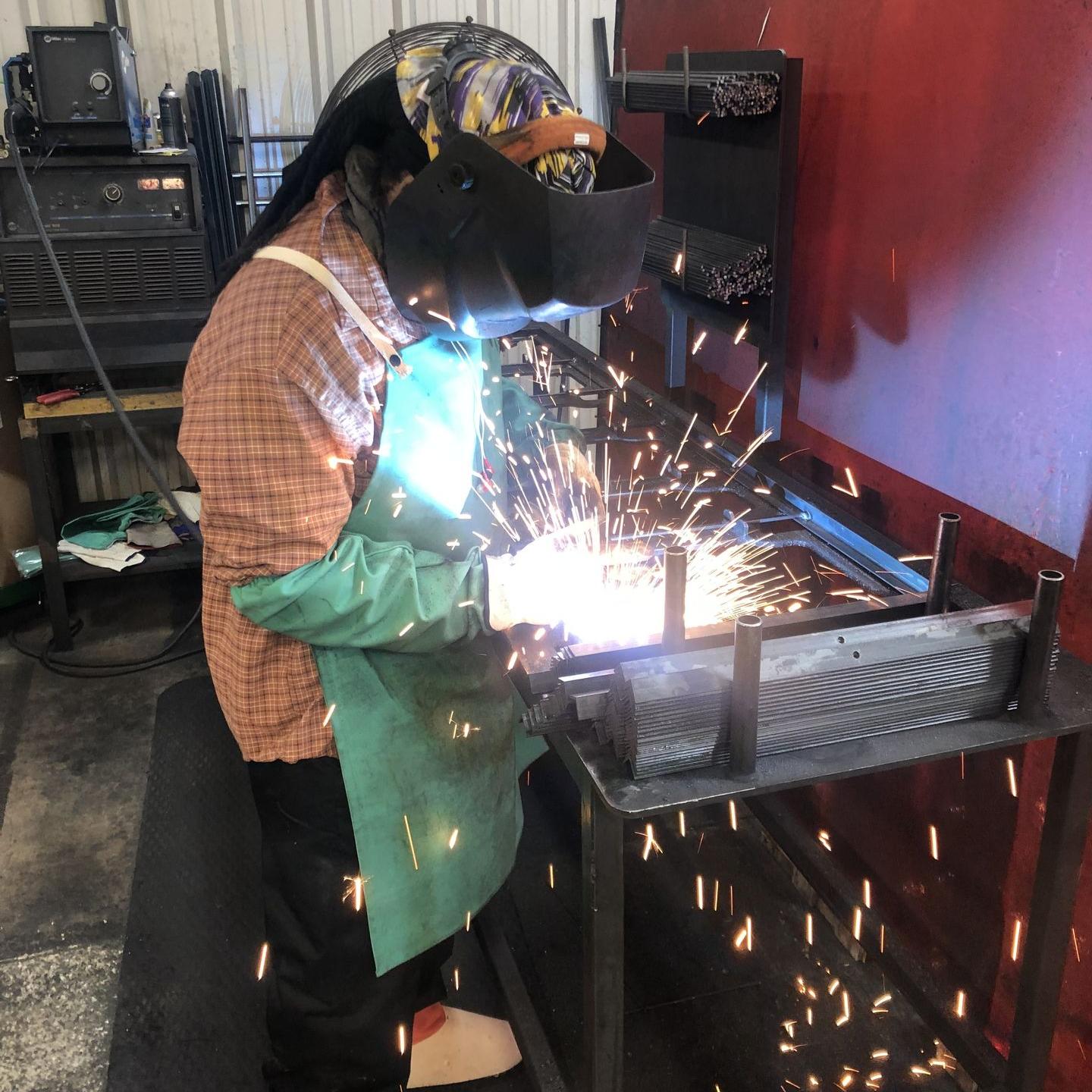
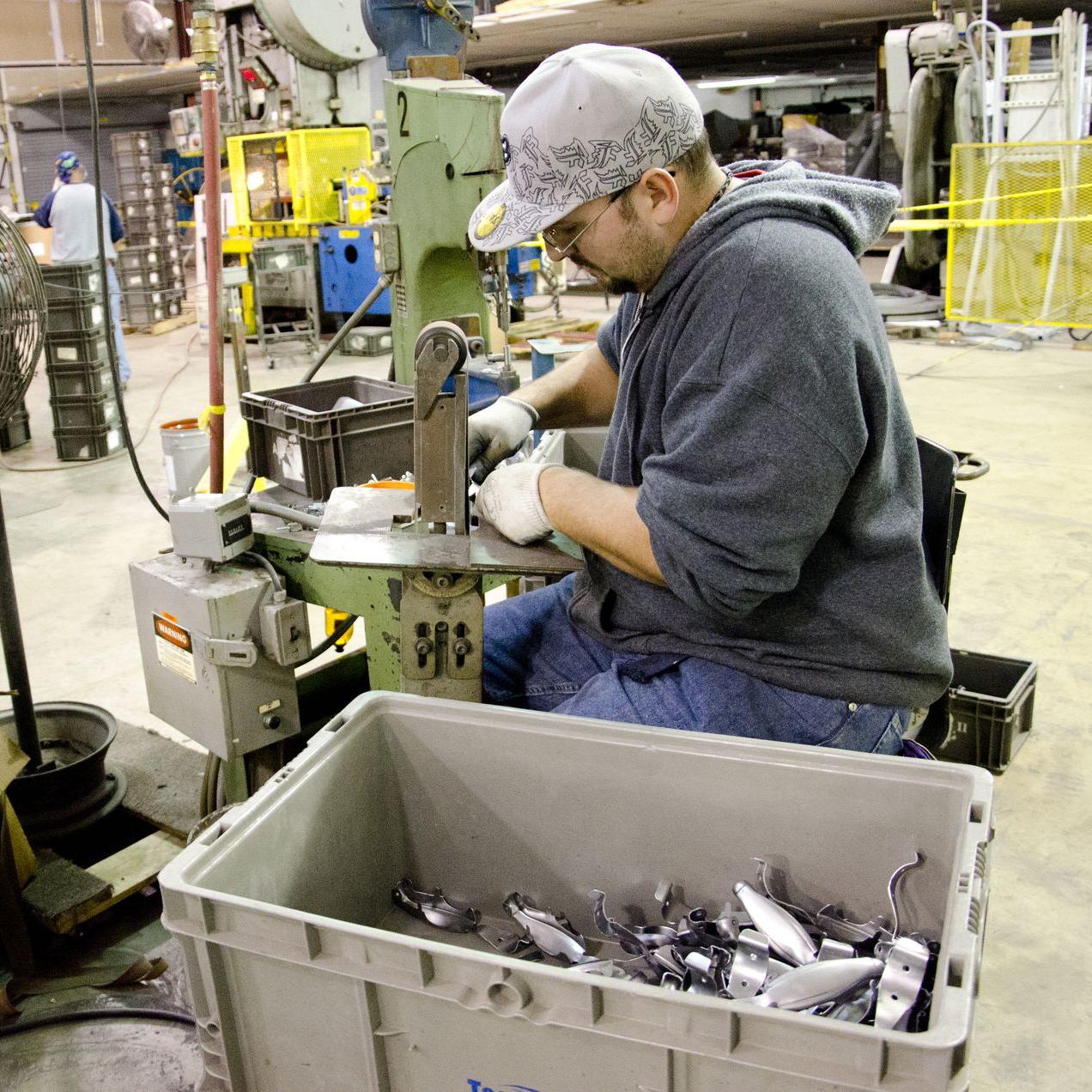
Small Component Manufacturing
At Thacker Caskets we take pride in every component that is used to make our caskets. We have invested heavily in manufacturing nearly all of our small casket components to ensure that we continue to offer competitive pricing and top-notch quality. We make nearly all of our hinges, brackets, and other small metal components that are used in the manufacturing process. Many of these parts require small stamping presses to form the metal into the shape that is needed for our production. By making these parts in-house we can pass on the savings and have better control over our inventory levels. All of these benefits ensure that we offer our customers an honest product at an honest price.